Transform Your Business Through Technology with Vision33
Manage every aspect of your business, including accounting, CRM, stock control, and production, with one integrated solution.
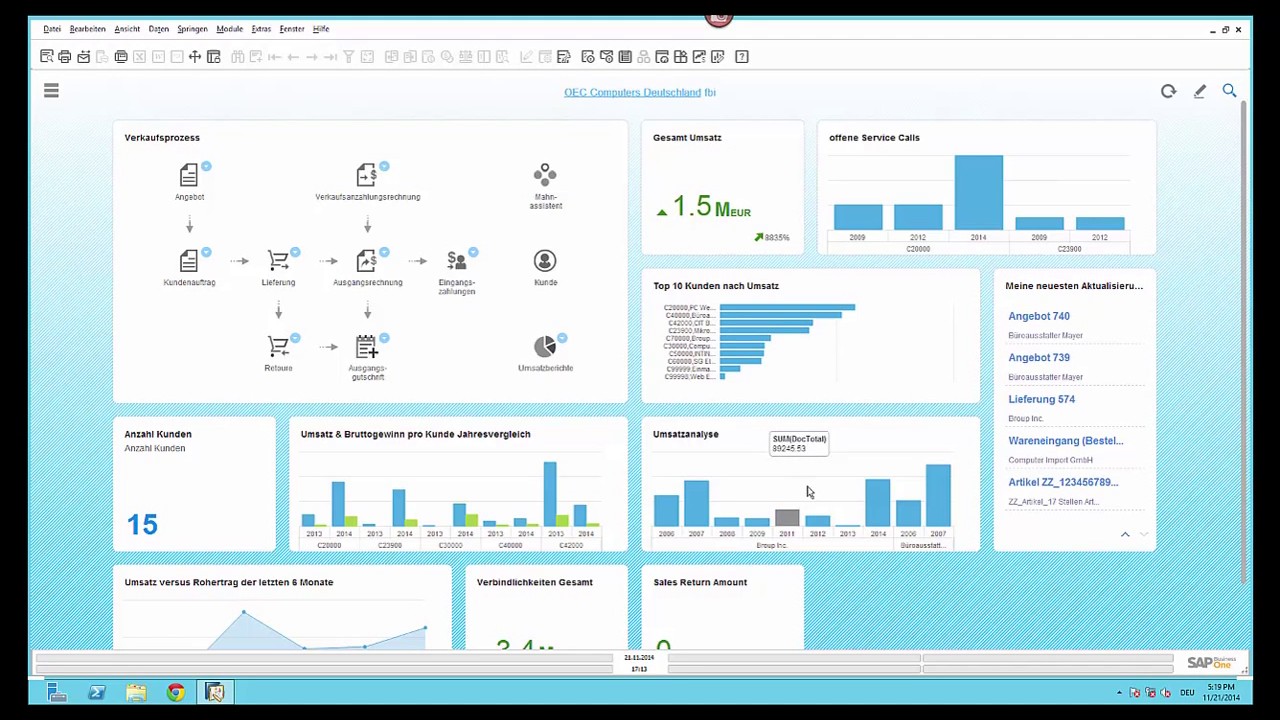
"Joining Vision33 was the best decision I ever made. I like working with brilliant people, and this company attracts some of the brightest in the industry."
Susan Martyn | General Manager, Enterprise
"I love the camaraderie within the team and the vast amount of industry knowledge the Vision33 team has."
Jarad Overturf | Director of Professional Services
"Vision33 is a progressive company that empowers employees to think outside of the box."
Romal James | Delivery Manager
"I started working with Vision33 eight years ago as a solutions advisor. Soon after, I moved into sales, and then onto working more closely with our clients alongside our implementation consultants. "
Bonnie Yiu | Sales Consultant




You're not alone. We've helped thousands of customers tackle their biggest problems.
Below are ten issues we’ve helped many of our customers resolve. Click on the boxes to explore each area and learn how one small change can improve your business and make life easier for your employees and customers.
Why Switch to Vision33
Shift your system challenges to our team.
At Vision33, hundreds of companies have come to us for service and support of their existing software systems. Because we’re much larger than the typical mid-market software and IT consulting firm, we have more to offer: more expertise, more experience, more coverage options, and more technologies. For example:
- TOTAL Care, our industry-leading support program, provides unmatched value and access.
- The Saltbox Platform provides integration and automation that drives growth.
- Our Customer Resource Centre and Wednesday Web Chats provide information, tips, and tricks to move your business forward.
Our mission says it all: We transform business processes and results for customers by delivering value through the promise of technology and its benefits for growing businesses. For over 30 years, Vision33 has helped companies integrate and automate their processes and applications to better serve their customers, employees, and stakeholders. Although the technologies have changed drastically in those 30 years, Vision33’s mission has never wavered.
Get in Touch to Learn More
Products
Click on the products below to learn how the right technology can transform your business.
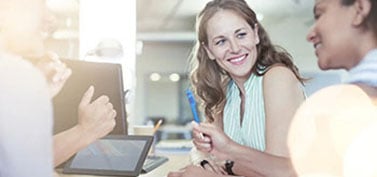

SAP Business One – An affordable, easy-to-use business management solution designed specifically for growing small to midsize businesses and subsidiaries.
Learn More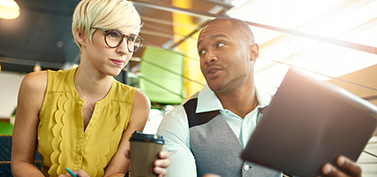

SAP Business ByDesign – An affordable, easy-to-use cloud enterprise resource planning (ERP) solution for fast-growing businesses.
Learn More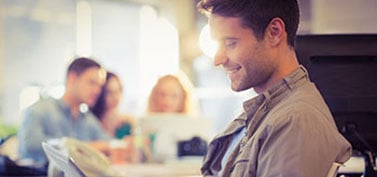
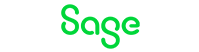
Sage Intacct – A flexible, configurable accounting software solution built on a true cloud foundation.
Learn More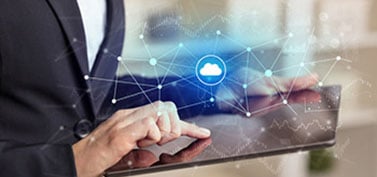
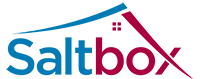
The Saltbox Platform: A cloud-native, low-code integration platform as a service (iPaaS) solution that breaks down data silos by integrating disconnected business systems like ERP, CRM, and eCommerce.
Learn More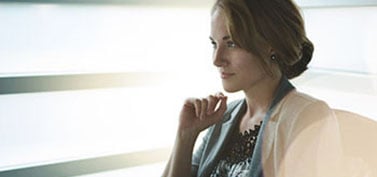

iDocuments – A browser-based solution that eliminates manual, tedious tasks and allows you to focus on innovation and growth.
Learn More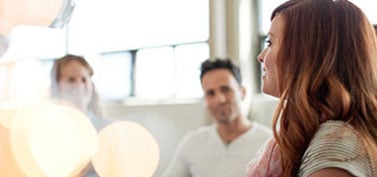
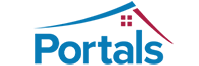
SAP Portals – Add-ons for SAP Business One that enable self-service access for employees & customers.
Learn More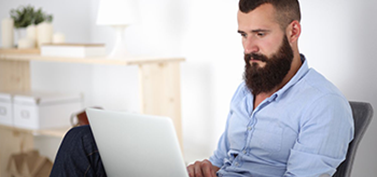

SAP S/4HANA Cloud provides automatic updates, keeps businesses competitive by streamlining operations, and offers real-time insights into business performance.
Learn More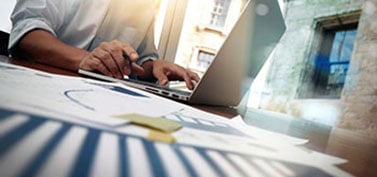
See all products – To learn more about Vision33's offerings, check out our ‘all products’ section.
Learn MoreCustomer Stories
Recent Blog
Vision33 Blog
.jpg)
.jpg)
.png)

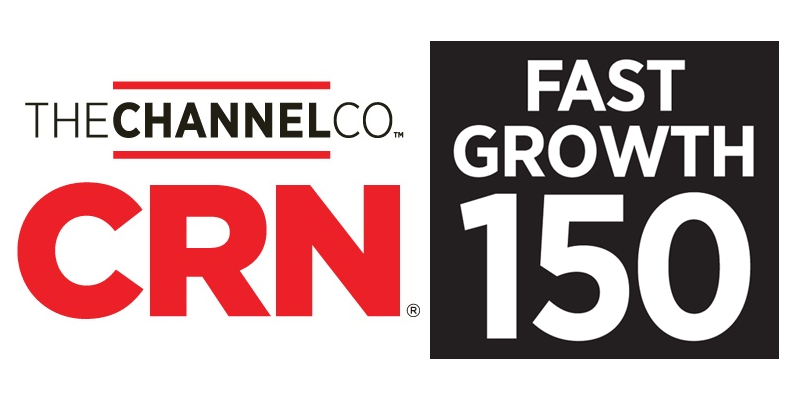
Let's Meet Your Challenge Together
Our resources, methodology, and project governance provide low risk for projects, free up your resources for other initiatives, and give you what you need to focus on where your business is going next.